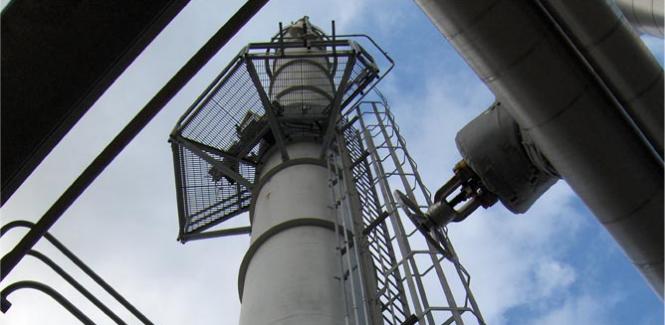
Stacks and Ductwork
Stacks and Ductwork are essential components that must be included on all boiler systems to route the hot flue gases to a safe location. Each project requires a custom engineered Stack and Ductwork set based on the volumetric flow rate of flue gas exiting the boiler, flue gas temperature, space constraints in the area, and optional inclusion of catalyst modules. Halgo Power engineers, models, and simulates the Stack and Ductwork set for each project to guarantee predictable and even flue gas flow through the system.
Economizer Supported & Freestanding
An economizer supported stack, also known as a “stub stack”, is mounted on and supported by an economizer, meaning that the stack is not anchored directly to the ground. It is ducted to and supported by the economizer and the underlying structural steel. Economizer Supported Stacks typically include multiple flu gas sampling ports that are accessible from the rooftop or a dedicated platform. A freestanding stack is an independent stack that sits on its own pad at a separate location from the boiler. It is anchored directly to the ground on a slab and requires ductwork to connect to the flue gas exit on the economizer. Stack height and strength is dictated by site specific information, and ladders, platforms, and sampling ports are often an included feature.
Horizontal & Vertical
All package boilers require ductwork pieces to route air and flue gas through the system. Horizontal and/or vertical ductwork and transition pieces can be custom designed to accommodate any tight or unique spatial constraints for each project. Halgo Power engineers ductwork pieces that include stiffeners in the appropriate quantities and locations to guarantee long term structural soundness. Ductwork is designed to be insulated in the field, if needed.
SCR Reactor House
The Selective Catalytic Reduction (SCR) Reactor House consists of a specially designed ductwork piece to hold NOx o catalyst material. The dimensions of the reactor house are determined by the amount and density of catalyst material required to meet the specified emissions requirements. Halgo Power will custom design and engineer this piece for each project.